
AFTERCARE
Lalegno’s Engineered Oak floors are really easy to keep clean and generally only require daily vacuuming. They don’t need to be damp mopped every day, and spot cleaning using a damp cloth after vacuuming will be sufficient in most cases.
A good clean every 2 weeks can be done using one of the LALEGNO CLEANER floor cleaning products we supply, using a microfiber mop.
​
Oil floors need to be re-oiled on average every 24 months depending on usage. This can be done quickly by a professional or DIY using a buffing machine and a clear oil. In between these re oils it is possible to buff surface scratches and dry spots with clear oil and or neat LALEGNO CLEANER and a microfiber cloth.
​
Lacquered floors don’t require any periodic maintenance. Between 5 and 10 years the floor can be re-sanded and sealed, depending on usage and ware. The floor does not need to be lifted. Sanding and re colouring takes place onsite.
Engineered floors can be sanded to rejuvenate and to change the colour. 3-4 times with a 4mm veneer, this is colour dependent.
FAQs
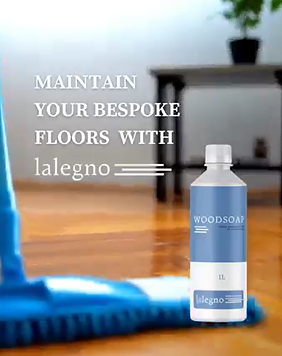
How to Use Our Wood Soap:
​
What type of floor should I use it for?
Our wood soap is developed for all of our Lalegno flooring.
​
What product is this?
This is a detergent specially developed for cleaning and protecting oak floors. It contains treatment oils and marine extracts that nourish and clean the wood at the same time.
​
When should I use it?
Every 15 to 30 days, for the overall maintenance of your floor.​​
​
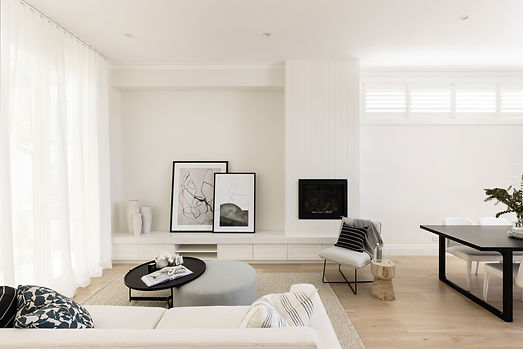
INSTALLATION
Pre-Installation Checklist and Preparation
-
Wood flooring is influenced by differences in moisture. It shrinks when dry and expands when wet. Before installing the floorboards, check the relative air humidity in the room. Ideally, it should be 50% to 60% all year through. Moisture measurements should also be taken on the subfloor and the levels should be in accordance with the SAWLFA specifications.
-
The sub-floor should be stable, even, level, dry and clean before installation. The allowable tolerances with regards to imperfections in the sub floor are 5mm in a perimeter of 3000 mm, and 3mm in a perimeter of 1800 mm.
-
Remove loose, flaky concrete by scraping it off by hand or sanding it down. Thoroughly vacuum the floor before starting the installation.
-
For floating installations, install an underlayment with a moisture barrier of at least 300 micron.
-
For glue down applications, a two-part moisture barrier should be applied to the concrete and allowed to dry for 24 hours before installation.
FLOATING INSTALLATION
As you would expect: with a floating installation, the floor is separate from the surface. The planks simply click together. A floating floor will move a little more and give a hollower walking sound - you can add a sound-absorbing subfloor. The efficiency of your underfloor heating also drops slightly. At the same time, it is somewhat cheaper and easier to lay a plank floor with this method. In addition, your floor can be dismantled.
Floating installation is not recommended for the following references: VERSAILLES, CUBE, HERRINGBONE and CHEVRON.
​
No experience with laying wooden floors yet? Then this might be the right choice.
​
When using the floating method, a suitable underlay, with suitable moisture barrier should be used. A 2-part rubber underlay with a 300-micron moisture barrier is recommended for optimal moisture protection and noise reduction of footfall.
​
Start the installation against a long, straight wall. Put the first-floor board down with the groove against the wall. Place a 15mm spacer between the wall and the board to keep the expansion seam open. This expansion gap needs to be maintained all around the room, including doorways, pipes, etc.
​
Lay the second-floor board in the extension of the first and push the short sided tongue and groove together. Tap the second panel into the first and make sure the seams are completely closed. The last floorboard of the first row has to be sawn to size. Complete the row with the sawn part and start the second row with the remaining piece of the floorboard.
​
The short pieces of two adjacent rows have to be spaced out as far as possible. To get a stable floor, the absolute minimum is 50cm. Make sure that the first two rows are perpendicular and well connected.
GLUED INSTALLATION
You can glue new oak floors directly onto high-quality screed or a solid subfloor. It is important to choose the right glue and to use the right technique. Gluing a wooden floor requires a little more skill, but the end result pays off. Because the glued wooden floor and screed become 1 whole, you have almost no walking noise.
​
Can you spare some time to lay your oak floor? Then a glued wooden floor is a solid option.
​
Need advice or do you want to call in a professional?
